Technical Resource
Undercarriage Components
Worn undercarriage components, particularly worn drive sprockets, will shorten track life and greatly increase the strain on track motors and gearboxes.
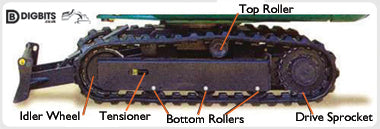
MINI EXCAVATOR TRACK FRAME
Identifying undercarriage components.
SPROCKETS
The sprockets should normally be replaced at the same time as worn out tracks. Effects of worn sprockets include:
- Accelerated track wear.
- Slipping in tracks causing shock loadings to drive motor.
- Increased likelihood of de-tracking and subsequent damage to tracks.
- Tearout of the metal inserts in a rubber track.
BOTTOM ROLLERS
Bottom rollers are designed to take transfer The majority the excavators weight and dynamic forces, through the tracks, and onto the ground. Check for wear on a regular basis. It is best to replace all the bottom rollers on one side. If only one roller per side is changed, then as the new roller may be slightly larger in diameter it will carry a higher load and have a shorter life.
Backlash or play in the bottom rollers will:
- Reduce the excavator’s stability.
- Increase the point loadings of less worn rollers, thereby increasing peak ground bearing pressure.
- Accelerate track wear.
- Increase the likelihood of de-tracking and subsequent damage to tracks.
- Increase the load on the track motor and gearbox.
TOP ROLLERS
The top rollers are designed to carry the tracks over the top of the track frame and are part of the tensioning system. Not all machines are fitted with top rollers - generally only diggers over 3 tonnes in
operating weight - smaller machines manage without them. The clearance
over the track frame afforded by the top rollers is useful in terms of allowing debris to fall free of the tracks, rather than becoming wedged between the track and the upper surface of the track frame.
Wear in top rollers if often neglected and they are only replaced when it is catastrophic, causing problems with:
- Loss of track tension.
- Increase the likelihood of de-tracking and subsequent damage to tracks.
IDLER WHEELS
The idler wheels are a fundamental component of the undercarriage. As well as transferring some of the track frame loads into the tracks, their key function is to feed the tension from the adjuster into the tracks. Failure will:
Reduce the excavator’s stability.
Result in a loss of track tension.
Increase the point loadings on rollers, thereby increasing peak ground bearing pressure.
Accelerate track wear.
Increase the likelihood of de-tracking and subsequent damage to tracks.
Increase the load on the track motor and gearbox.